
SKIN-ON-FRAME
Traditional, lightweight & robust
Skin-on-frame boats can be built with minimal use of resources and offer some interesting craft features such as steam bending or skin and sewing the wooden frame. A modern alternative is the fuselage frame construction method, which uses transverse frames made of sheet material instead of steam-bent ribs.

Wood
High tech material from the forest
In traditional skin-on-frame boat construction, the gunwales define the sheer and provide the main structural support for a skin-on-frame boat. The transverse ribs, which are steam-bent from narrow wooden strips, are attached to the gunwales. The ribs support the stringers, which determine the shape of the outer skin and are responsible for the typical chined shape. Everything is connected with artificial sinew and wooden dowels. Nails, screws or adhesives are not necessary. The gunwales and stringers are made of the lightest possible wood. Red Cedar is particularly suitable for this purpose, as it is very homogeneous, knot-free, light and easy to work with. In addition, its high resistance to rot and fungal attack should be emphasized. Other woods such as spruce, pine or Douglas fir can of course also be used. The ribs are made of ash or oak. Ash wood has the advantage over oak that even kiln-dried wood is still suitable for steam bending.
The Gunwales
In a canoe, the gunwales are equivalent to the coaming; in a skin-on-frame kayak, the gunwales are located at the transition from the hull to the deck. They carry most of the forces acting in a skin-on-frame boat. In kayak construction, they are usually set at an angle of about 17° and thus naturally produce the typical sheer as well as the trapezoidal cross-section of the hull. In canoes, the gunwales are glued together from several strips to form the desired sheerline, since the shape of the hull requires vertically positioned gunwales. Placing the gunwales at an angle, as in the kayak, is not an option here. The gunwales are provided with pockets on the underside, in which the ribs are attached. Since the gunwales are important statically, a careful choice of wood is important. Red Cedar is the best choice, as the wood is very strong and resistant to rot in relation to its light weight. It is also very easy to work with hand tools and can usually be obtained knot-free. A board with lying annual rings results in gunwales with lying annual rings (see photo).


Steambending
Finding wood suitable for steam bending is the first challenge in skin-on-frame canoe or kayak construction. Ash and oak are particularly suitable, but the wood should ideally be undried. On the market, almost exclusively kiln-dried wood is offered, which is why you should look at the beginning of the supply chain: in the sawmill. For all those who are now thinking that this all sounds very stressful: unlike oak wood, ash wood has the property that it can still be steambent well even when kiln-dried. A little more breakage must be accepted here, however, so to be on the safe side you should buy a little more wood than calculated. Ideally, you will find boards with standing annual rings, from which you can saw strips with lying annual rings on the table saw (see photo). It is important to always saw parallel to the annual rings. Strips in which as many annual rings as possible run from the beginning to the end are particularly strong and less likely to break.
Lashing the Frame
The lashing of wooden parts is an old joining technique, which was realized with animal sinew or plant fibers in ancient times. Today, in skin-on-frame boat construction, waxed artificial sinew made of polyamide (nyln) is used. Lashing has the advantage over doweling, nailing or screwing that the construction has a better tolerance to impact because the frame of a skin-on-frame boat remains flexible. Where a glued joint would break, the lashed joint remains intact. The stiffness of a Skin-on-Frame canoe hull depends primarily on the strength of the lashing. It is therefore very important to keep the sinew under high tension at all times while lashing the frame. A waxed string has the advantage here that it already sticks to itself, making it easier for the boatbuilder to maintain the tension. A very tightly lashed frame is less likely to become a "banana" later due to the forces that occur while skinning.

Your biggest sewing project.

Skinning
The skin turns the frame into a boat. Polyamide (PA), also known as "nylon", polyester (PES) but also cotton are suitable. Polyamide is the most robust material and can be varnished well with polyurethane varnishes. A major disadvantage, however, is the characteristic that polyamide absorbs water and expands. Even careful varnishing cannot change this. Skin-on-frame canoes covered with nylon can look wavy in damp or cold weather because the skin loses its tension. This can be countered by soaking the fabric in water while skinning and sewing it under high tension. When it dries, it stretches even tighter around the frame. Caution is advised, however, as there have been reports of canoe frames breaking under the contracting, drying skin. Polyester, on the other hand, does not absorb water, so it does not become slack. Compared to nylon, however, it's not quite as robust. Another advantage of polyester is that, unlike nylon, it can be shrunk with an iron. So it does not have to be skinned under extreme tension, but can be shrunk later and retains this tension. When choosing a fabric, the weave type is also important: in relatively loosely woven fabrics such as "Ballistic Nylon", the seam quickly pulls large holes in the fabric that cannot be sealed with varnish. Other, more compactly woven fabrics are better suited here. This should be tested beforehand... The easiest way to skin a canoe is to simply attach the skin to the gunwales with stainless steel staples. The staples are later covered by a wooden strip. Sewing is only necessary along the stern and bow of the canoe.
"Erster Eindruck: das Boot sieht gut aus und wiegt beim Tragen beeindruckend wenig. Es sieht dennoch absolut stabil und solide aus. Dann auf dem Wasser: Durch den großen Süllrand ist der Einstieg leicht. Ich sitze tief, habe angenehm viel Platz für Beine und Füße. Rückenlehne und Fußstützen sind genau da, wo sie sein sollten. Auf den spartanischen Holzsitz würde ich mir auf Dauer lieber ein Polster legen. Die Knie haben guten Kontakt unter dem Süll. Meine anfängliche Scheu, die Fersen einfach aufa die dünne Bootshaut zu setzen, vergesse ich schnell. Auch wenn man drinsitzt, wirkt das Boot ausgewogen und solide konstruiert, trotz des leichten Gerüsts und der für mich ungewohnt dünnen Außenhaut. Die ersten Paddelschläge: Das Boot liegt durch die tiefe Sitzposition stabil und fährt sich leicht, mit sehr gutem Geradeauslauf. Zum Steuern lässt es sich gut ankanten und geht willig in die gewünschte Richtung, allerdings mit recht großem Kurvenradius, wie bei der Länge und dem geringen Kielsprung nicht anders zu erwarten. Es gab nur wenig Wind, aber bei ein paar leichten Böen konnte ich keine Windanfälligkeit spüren – die Bordwände und Decks sind niedrig genug. Etwas kräftiger gepaddelt, da zieht das Boot beeindruckend schnell und leicht los. Ankanten, mit oder ohne Fahrt, bis das Wasser am Süllrand steht, ist kein Problem. Das Boot zeigt eine hohe Endstabilität, auch ohne stärkeres Stützen. Mein Fazit: Ein sehr angenehm und mühelos zu fahrendes, leichtes und schnelles Boot. Die Bauanleitung und Baupläne sind professionell gemacht. Auch die Bausatzteile sehen sehr gut aus. Die Preise dafür sind fair kalkuliert. Ob ich es schaffe, dieses schöne Boot selbst zu bauen? Im Winter werde ich es ausprobieren!" Jost, 179cm, 67kg - hat das NANOOK getestet und baut nach dem Bauplan
Varnish & Pigments
A nice way to customize a skin-on-frame canoe is a colorful varnish. Hereby, many tones can be realized, from cool blue or green to warm red or orange tones. Homogeneous to patinated looks can be created by thorough mixing or a streaky finish. Natural earth or mineral pigments are added to the hardener of the varnish to achieve a uniform color throughout the entire varnishing process. The color shade and, above all, the desired opacity should be tested on a test piece beforehand. For this purpose, it is advisable not to mix too small quantities of paint and pigment, since the weight proportions are difficult to transfer to larger quantities. Polyamide and polyester are coated with polyurethane varnishes. Boats covered with cotton can also be coated with oil-based varnishes.
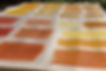

Lightness
The fascination of a skin-on-frame canoe, besides its light weight, is the transparent skin through which the sun shines, making the frame visible to the outside as well. When paddling, you can also see the waterline sloshing through the skin and can see lily pads passing under the boat. For those who find the strip construction method too glossy and labor intensive, the skin-on-frame construction method is recommended. The more traditional steps, less likely to escalate into monotonous labor, reward with new experiences in steam bending, lashing and sewing. The result is a delicate-looking, yet robust boat that is suitable for everyday use and, like my "SOFi" model here at Lake Rolstropasjön in southern Sweden, integrate perfectly into the landscape.