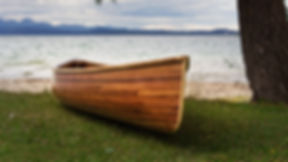
DIE LEISTENBAUWEISE
Elegant, klassisch, zeitlos
Holzkanus in Leistenbauweise sind leichte und robuste Boote mit einem hohen Gebrauchswert und einer eleganten Optik. Die Kompositbauweise aus Holzleisten und GFK stellt keinen Kompromiss zwischen Optik und Gewichtsvorteilen dar, sondern ist meistens sogar leichter als andere Materialien im Kanubereich. Je nach verwendeten Hölzern und Gewebegrammaturen können Kanus mit einem Gewicht von weit unter 20kg realisiert werden.

Die Helling
das Fundament mit dem alles beginnt. Standfest, eben und "im Wasser".
Jeder Bau eines Leistenkanus beginnt mit einer Helling. Sie ist das formgebende Gerüst, auf der die Rumpfleisten verleimt werden. Da auf der Helling die Mallen angebracht werden und die Symmetrie des Kanus von ihr abhängen, sollte sie gerade ausgerichtet und zudem sehr stabil sein. Über den Mallen werden später die Rumpfleisten angebracht und verleimt. Die Mallen werden nach dem Bau des Kanus wieder entfernt und können, genauso wie die Helling, wiederverwendet werden.
Leistenproduktion
Was es zur Produktion von 70 Rumpfleisten zu sagen gibt: danach kennst du deine Säge.
Das ideale Holz für ein Holzkanu in Leistenbauweise ist Red Cedar (Thuja plicata), da es sehr leicht ist, eine wahnsinnig schöne Optik hat und zudem sehr einfach zu verarbeiten ist. Ein weiterer Vorteil des Holzes ist der aromatische Duft, den es beim Aufsägen, Hobeln und Schleifen abgibt. Bei der Verarbeitung sollte bei diesem Holz allerdings dringend eine Filtermaske getragen werden, da die Stäube gesundheitsschädlich sind. Allein bei der Herstellung dieser 6mm starken, etwa 20mm breiten, konkav und konvex gefrästen Rumpfleisten werden auf Säge und Frästisch mehrere hundert Meter zurückgelegt. Die gesägten Leisten werden schließlich an den Seitenkanten noch mit einer konkaven und einer konvexen Fräsung versehen, durch die die Leisten sich auch winklig verleimen lassen. Zum Fräsen kommt ein Rolladenfräser zum Einsatz, der sowohl die konkave als auch die konvexe Kontur aufweist.

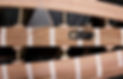
Beplanken
Leiste für Leiste, mit oder ohne Tacker. Am Ende ist Fingerspitzengefühl gefragt, wenn der Rumpf am Kiel geschlossen wird.
Eine grundlegende Entscheidung sollte bereits vor dem Anbringen der ersten Leiste getroffen werden: "mit oder ohne Tacker?" Das Tackern der Leisten an die Mallen hat den Vorteil, dass der Rumpf schneller fertiggestellt wird, da Leiste für Leiste angebracht werden kann ohne die Trocknungszeiten des Leims einzuhalten. Optisch hat diese Methode allerdings den Nachteil, dass auf dem Rumpf später in gleichmäßigen Abständen Bahnen von kleinen Tackerlöchern zurückbleiben. Besser, aber auch aufwändiger, ist der Bau ohne Tacker, zu dem es unzählige, mehr oder weniger umständliche Herangehensweisen gibt. Ich empfehle statt Tackern stellenweise und nur wo nötig Schrauben in vorgebohrte Löcher zu setzen und die Schraublöcher später mit Holzdübeln zu schließen. Schrauben deshalb, da wenige Schrauben mehr Kräfte aufnehmen müssen als viele Tacker. Ein paar unregelmäßig positionierte Holzdübel fallen am fertigen Kanu fast nicht auf und verleihen dem Rumpf zudem eine Art traditionellen Look wie bei Klinkerbooten. Leimreste sollten immer zeitnah mit einem feuchten Lappen entfernt werden, da eingetrochnete Leimnasen später das Schleifpapier zusetzen und den Schleifprozess erschweren. Zum Kiel hin entsteht schließlich ein ovales Loch, das mit immer kürzer werdenden Leisten geschlossen werden muss. Die letzte Leiste wird als "Whiskey-Plank" traditionell mit Whiskey begossen. Beim Bau eines Leistenkajaks werden Rumpf und Deck auf der gleichen Helling hergestellt, jedoch werden die beiden entstandenen Schalen getrennt geschliffen und laminiert, bevor sie später zum fertigen Kajak verklebt werden. Das Verkleben der beiden Schalen durch die kleine Cockpitöffnung ist sehr anspruchsvoll und verlangt viel Fingerspitzengefühl.
Schleifarbeiten
...sind Fleißarbeiten. Ob du über die nötige Ausdauer und Geduld verfügst, weisst du spätestens danach.
Schleifarbeiten nehmen vom gesamten Bau eines Leistenkanus die meiste Zeit in Anspruch und verlangen vom Kanubauer einiges an Geduld und Durchhaltevermögen. Die ganze Schönheit des fertigen Kanus hängt allerdings maßgeblich von der Qualität der Schleifarbeiten ab, daher solltest du dir hier viel Zeit nehmen. Der geschlossene Rumpf bleibt vorerst auf der Helling. Für einen groben Vorschliff ist auf der Aussenseite ein Exzenterschleifer gut geeignet. Wichtig ist ein gleichmäßiges, flächiges Arbeiten. Zum Entfernen von Leimresten ist man geneigt, den Schleifteller anzukanten, was unbedingt zu vermeiden ist, da hierdurch tiefe Dellen entstehen können, die auch noch am fertig laminierten Kanu zu erkennen sind. Der Feinschliff erfolgt nicht zu fein mit Korn 120 oder 180, damit das Epoxidharz später eine Struktur zum Haften findet. Das Schleifpapier wird auf einer großen, nicht zu weichen Schleifunterlage befestigt, die sich den Konturen des Rumpfes anpasst. Per Hand wird nun in Faserrichtung des Holzes geschliffen, bis sich eine gleichmäßige Oberfläche ergibt. Den Fortschritt begutachtest du am Besten im Streiflicht. Schließlich wird der Rumpf einmal feucht abgewischt, damit sich die Holzfasern aufstellen. Diese werden in einem letzten Feinschliff entfernt und der Rumpf ist fertig zum Laminieren. Nach dem Laminieren der Aussenseite wird die Innenseite geschliffen. Hier kann am Boden des Rumpfes vorsichtig der Exzenterschleifer zum Einsatz kommen. Ansonsten ist das Innere des Rumpfes größtenteils Handarbeit. Je nach Radius solltest du dir hier verschiedene Unterlagen fürs Schleifpapier suchen, die auch in den Radien einen gleichmäßigen Schliff erzeugen.
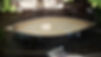
Vom Holz zum Glas.

Laminieren
durch den Auftrag glasfaserverstärkten Kunststoffes wird der filigrane Holzrumpf zum robusten und nutzbaren Kanu.
Zieh deine Gasmaske, Overall und Handschuhe an... es geht los!
Das Laminieren eines Holzrumpfes mit Glasfaserverstärktem Kunststoff (GFK) ist eine von vielen Kompositbauweisen im Bootsbau und hat im modernen Holzkanubau eine große Bedeutung bekommen. Wie filigran und zerbrechlich ein Kanurumpf ist, merkt man, wenn man den rohen Holzrumpf einmal von der Hellig nimmt: schätzungsweise 20% der Entstabilität kommen aus dem Leistenrumpf, 80% aus dem GFK. Das Holz ist also die Komponente, die dem Kanu die Form und die Optik verleiht, jedoch nicht die Stabilität. Auf den gesäuberten Rumpf wird nun eine Glasfasermatte aufgelegt und mit einem kleinen Handbesen glattgestrichen. Das Gewebe sollte mit Baumwollhandschuhen angefasst werden, damit es keine Fettflecken bekommt, an denen das Harz später nicht mehr haftet. Gewebe in Köperbindung eignen sich besonders gut für Holzkanurümpfe, da sie sich besser über Konturen legen lassen als Gewebe in Leinwandbindung. Zum tränken des Gewebes kommt ein Epoxidharz mit langer Topfzeit zum Einsatz, damit genug Verabeitungszeit bleibt. Es wird von einer Rumpfspitze zur anderen gearbeitet. Mit einem großen Pinsel wird das Harz aufgetragen und einige Zeit ins Holz einziehen lassen. Hierzu sollte das Harz nicht zu sparsam aufgetragen werden, da ansonsten trockene Stellen entstehen können, wenn das Holz sehr durstig ist. Ist das Holz gesättigt, wird überschüssiges Harz mit einer Spachtelklinge aus Kunststoff vorsichtig abgezogen und entsorgt. Hierbei ist der richtige Druck und der richtige Winkel der Spachtelklinge entscheidend. Bei zu geringem Druck wird zu wenig Harz entfernt und das Gewebe könnte im Harz aufschwimmen, wodurch Unebenheiten entstehen können, in die man später hereinschleift. Wird zu viel Harz entfernt, ist das Gewebe zu trocken und es entstehen weiße Flecken im Laminat, die auch am fertigen Kanu sichtbar sind.
Fillcoats
Nachtschicht in der Kanuwerkstatt. Das Laminat wird in vielen dünnen Schichten aufgebaut. Nun ist das Harz dein Arbeitgeber und entscheidet, wann du schlafen darfst.
Der erste Laminierdurchgang dient dem Tränken des Gewebes und sorgt für eine Haftung des Gewebes am Holz. Nachdem das überschüssige Harz mit dem Spachtel abgenommen wurde, ist die Gewebestruktur wieder sichtbar, die nun mit mehreren "Fillcoats" gefüllt werden muss. Der Zeitpunkt für den ersten Fillcoat ist gekommen, wenn das Harz noch klebrig ist, aber keine Fäden mehr zieht. Teste dies nicht mit deinem nackten Finger, sondern mit einem Nitrilhandschuh! Die Fillcoats können langsam mit einer lösungsmittelverträglichen Schaumwalze aufgebracht werden. Rollst du zu schnell, bleiben kleine Luftblasen im Harz zurück, die du zeitnah und vorsichtig mit einem Heißluftgebläse entfernen kannst. Trage so viele Fillcoats auf, bis sich eine ausreichende Schicht Harz aufgebaut hat, damit ein späterer Schliff möglich ist. Hierbei solltest du auf keinen Fall ins Gewebe schleifen, da sonst weiße Stellen zurückbleiben. Weitere Tipps zur Verarbeitung von GFK und dem Arbeitsschutz findest du im Blog.
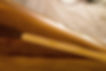
Vorfreude
Der Einbau der Sitze bringt sich dem Wasser näher. Du spürst, dass es bald losgeht und dich die erste Fahrt mit deinem selbstgebauten Kanadier für alle Mühen entlohnt!
Erkennbar ist nun ein fast fertiger Rumpf. Nach all den Stunden des Schleifens und der Arbeit mit Harzen und Gasmaske würde man einfach gerne den halbfertigen Rumpf probepaddeln, jedoch fehlen noch die Einbauten. Ein Kajakrumpf besteht aus zwei Schalen, die miteinander zum fertigen Kajak verklebt werden müssen. Anschließend werden der Sitz, Fußstützen und Luken eingebaut. Beim Kanadier werden die Dollborde am Süllrand angebracht und in der Bootsmitte durch eine Ducht verbunden, was dem Rumpf seine Steifigkeit verleiht. Die Sitze werden eingebaut und schließlich kann der Rumpf lackiert werden. Beim ersten Paddelausflug passiert es dann plötzlich: der erste Kratzer ... das Kanu ist nun fertig!
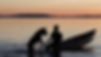
ist es dein Projekt?
Handwerklich ist die Leistenbauweise äußerst anspruchsvoll, da nicht nur präzises Arbeiten beim Beplanken, sondern auch eine saubere Verarbeitung beim Laminieren und Lackieren des Rumpfes nötig sind. Neben den nötigen handwerklichen Qualitäten ist bei vielen Arbeiten außerdem viel Ausdauer bei großflächigen Schleifarbeiten nötig. Das Ergebnis rechtfertigt allerdings alle Mühen: zum ersten Mal mit dem eigenen Leistenkanu zu paddeln ist unbeschreiblich.